by Ishaan Goel
INTRODUCTION
In 2020, hydrogen shot to the forefront of the renewable energy conversation, with stakeholders making major investments in its growth. The European Union has allocated nearly EUR 400 billion to hydrogen within its Covid-19 recovery package, to ramp up production capacity ~150 times by 2030. Globally, hydrogen production projects under development have nearly tripled (by capacity) with several firms announcing ambitious gigawatt-scaled ventures.
The appeal of hydrogen stems from its excellent capabilities as both an energy carrier and storage medium. Beyond its extensive usage in high-temperature industrial processes and manufacturing, it shows potential in areas that have proven difficult to decarbonize. These include central heating systems in buildings and fuel for heavy transportation. Hydrogen can also help solve key problems for powering the electric grid with only renewable power, like long term energy storage to smooth seasonal fluctuations in supply and demand.
Lowering the cost of hydrogen is important to ensure that it becomes competitive with fossil fuels. The Hydrogen Council estimates that prices have to reach $0.5-2/kg, to compete with natural gas and coal. One key component of this cost is how the hydrogen is actually manufactured.
Hydrogen gas does not occur naturally in our environment, so it must be obtained from other molecules that contain the element. The most common sources are water (H2O) and methane (CH4) in natural gas.
GREEN AND CLEAN
Electrolyzers pass an electric current through water, splitting it into hydrogen and oxygen. The current can in turn be generated from renewable sources, making the entire process carbon-free. The hydrogen thus obtained is called green hydrogen.
With virtually no emissions, this is the cleanest way of producing hydrogen. However, green hydrogen is yet to become widespread due to its unviable price. Advancements in electrolyzer technology have caused significant reductions in their capital costs in recent years, but they remain quite expensive.
These costs can be considerably reduced by expanding the production of electrolyzers to achieve economies of scale. According to a report by the International Renewable Energy Agency (IRENA), reaching 1 GW/year of electrolyzer production (by capacity) can decrease the prices of components between 30-85%. On average, overall production costs can reduce by about 18% every time the total capacity of electrolyzers doubles due to competitive innovation by firms.
Such a drastic increase in capacity must be accompanied by a comparable increase in the supply of renewable electricity. One widely proposed method to minimize these power costs is to produce hydrogen using the surplus power when there is a peak in renewable supply (such as during strong winds or sunlight). This surplus cannot be taken into the grid and would have otherwise been wasted, so is available at very low cost for the electrolyzers.
However, these periods of excess only occur a small fraction of the time. While the electrolyzer units installed would be designed with enough capacity to accommodate these large peaks, they would remain unused a majority of the time. A 2015 study in the IEEJ Energy Journal estimates that the average production would only be 8-17% of the maximum potential.
So, the initial capital investment would be distributed over a much smaller amount of hydrogen produced, which would increase the end-cost of hydrogen. Any reductions in capital costs achieved through scale may be dampened for consumers.
This is seen in the left graph in Figure 1 below. Even when average capital costs are reduced almost 75% by scaling to $200/kW, renewable electricity would have to be cheaply available at $20/MWh for at least 5-6 surplus hours per day to be comfortably within the $0.5-2/kg price range.
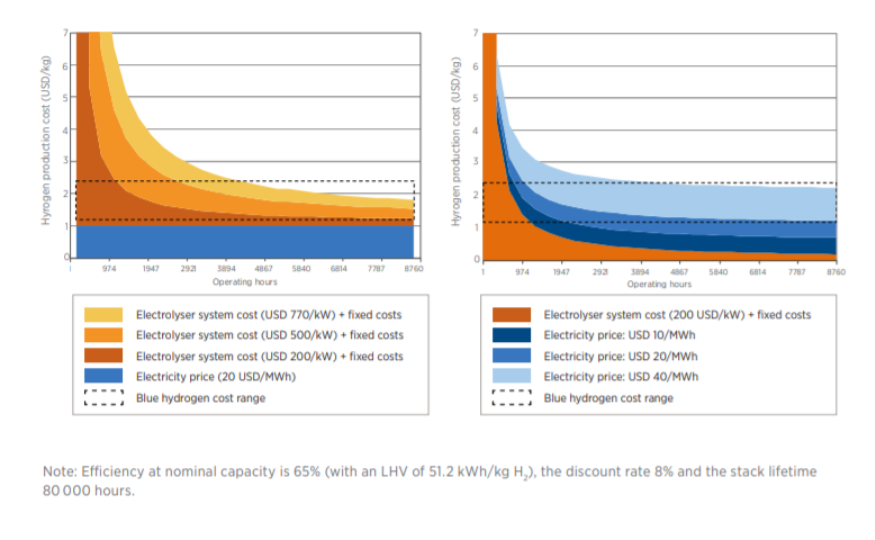
Electrolyzers could be made to utilize power throughout the day whenever available, including non-surplus hours. This would only partially alleviate the issue of capital underutilization as renewable sources face large daily fluctuations, which may also degrade the electrolyzers over time.
Battery storage or grid-electricity could be used to stabilize renewable power and supplement off-peak supply, which will ensure that electrolyzers always operate close to their maximum capacity. Both options decrease the capital investment required to produce each unit of hydrogen, but significantly raise the power purchase cost. The end-cost would now depend more on electricity prices, which can be made cheaper through appropriate policies and market structures. Note that this is not desirable for highly carbonized grid-electricity.
This is shown in the right graph of Figure 1. Assuming capital costs are scaled down substantially to $200/kW, electricity prices between $10-20/MWh are needed for green hydrogen to become competitive with conventional hydrogen. For reference, solar power is now available at $20-60/MWh, depending on the country.
FOSSIL-FUELLED HYDROGEN
95% of hydrogen is presently produced through a process called ‘steam methane reformation’ (SMR). Methane and steam react to yield carbon monoxide and hydrogen. The carbon monoxide further reacts with steam to produce more hydrogen and carbon dioxide. Instead of pure methane, industrial processes generally use natural gas (~90% methane). This hydrogen is called grey hydrogen.
From a thermodynamic perspective, it is easier to convert natural gas into hydrogen than into a comparable amount of electrical energy. Hydrogen yields about 33.6 kWh of energy per kilogram. The amount of natural gas required to produce 1 kg of hydrogen comes out to be 2-3 times smaller than the amount required to produce 33.6 kWh of energy.
With the existing infrastructure and scale of the natural gas industry, the average cost of hydrogen from SMR is about $1-3/kg. In comparison, green hydrogen on average costs 3-5 times more at about $4-8/kg (both ranges were estimated from market sources).
The advantage of SMR over electrolysis is particularly pronounced in end-use applications like steelmaking, which require hydrogen. Renewable power may not be readily available near industries and produces more expensive hydrogen, so SMR provides the cost-effective option.
When the end-use application is transportation, the requirement to convert the hydrogen back into electricity using expensive and relatively inefficient fuel cells mean that batteries or direct internal combustion of natural gas are more economical than steam reformation in most situations.
THE COSTS OF CARBON CAPTURE
SMR is not inherently carbon-free, but the carbon dioxide produced can be collected and stored. This is called carbon capture & sequestration (CCS), and hydrogen produced through the SMR-CCS combination is termed blue hydrogen. With appropriate carbon-storage techniques, it can be as clean as green hydrogen.
CCS is essential for decarbonization, but it represents an added capital investment for manufacturers and affects the entire supply chain. As shown in Figure 2, depending on region, it can increase the cost of hydrogen by 30-55%, which reduces its relative advantage over green hydrogen.
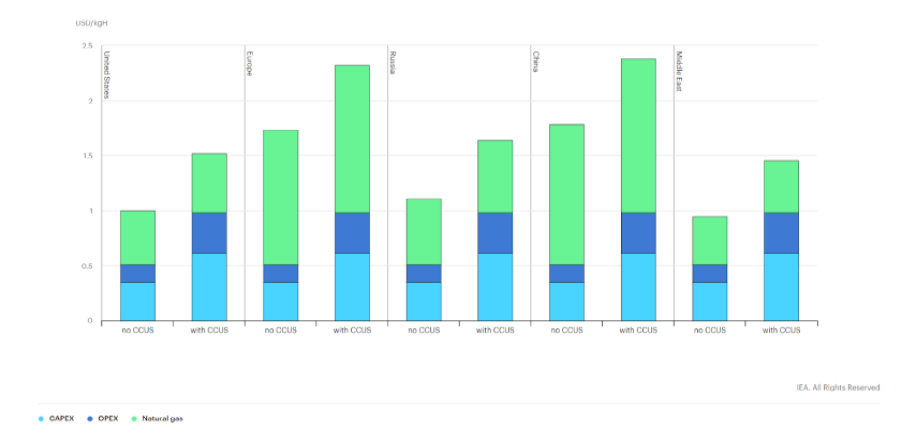
Being non-essential to the actual production process, CCS must be promoted through uniform regulation like stringent pollution-control requirements. Low-expense CCS techniques will need to be developed if blue hydrogen is to be competitive with fossil fuels.
Current carbon-management options include injection into underground geological formations, storage as minerals and carbonate compounds or enhancing the recovery of oil. All of these methods are currently very costly. Although cost-effective, using CO2 to enhance oil recovery in oil-wells is also counter to the goal of decarbonization.
BIG OR SMALL, NEAR OR FAR
Beyond the method, the organization of the production facilities for hydrogen is important for economics. There are 2 primary ways in which to organize the production system for hydrogen.
Centralized production involves extremely large facilities that meet hydrogen demands for vast geographical regions. These can leverage economies of scale and efficient methods to considerably decrease production costs. The facilities may be distant from the target location of the hydrogen, and closer to natural gas processing plants or renewable sources to acquire input materials more easily.
The largest electrolysis plant currently operational is in Fukushima, Japan, which uses a 20 MW solar generation facility to power a 10 MW electrolyzer unit. IRENA has classified plants of this scale in the first stage of electrolyzer deployment, with the last stage envisioning units greater than 100 MW each.
Distributed production involves small, localized facilities close to (or at) the target locations. These cannot achieve economies of scale or the same level of efficiency as centralized systems, which limits their ability to cut down production costs. However, their proximity to target locations considerably reduces the cost of transporting hydrogen, and facilitates integrated production-application systems.
This points towards a key-tradeoff between distributed and centralized facilities – that of electricity transmission and hydrogen distribution costs. Moving hydrogen by road from central facilities to target locations can be quite expensive, because of its low energy per unit volume (4 times lesser than gasoline) and extensive safety requirements for the vehicle. Constructing pipeline networks for hydrogen would be very capital-intensive, with each mile costing an estimated $250,000-1,000,000. However, distributed production requires connections of renewable energy to each facility, and transmission rates are highly dependent on the regional regulations and tariff rates.
The choice between distributed and centralized facilities depends on many other factors. Smaller plants would require lesser capital initially to establish, which would allow them to be set up in greater numbers. For instance, distributed facilities could be placed at every refueling station for hydrogen-based automotives. On the other hand, CCS techniques are cheaper when implemented at larger scales, which might inhibit their use in small facilities.
Large, central facilities can be combined with end-use industries to form ‘hydrogen valleys’, where the entire supply chain of hydrogen – from production to final application – is concentrated in one geographical area. This would reduce input costs for all goods produced in the valley, while also largely eliminating hydrogen distribution costs. Further, CO2 from SMR could be managed by channeling it into industries like methanol, cement and indoor agriculture (greenhouses).
The idea of using existing gas pipelines for hydrogen distribution has gained traction because it eliminates the need for large investments in specialized hydrogen transport infrastructure. It is also an efficient way to prolong the utility and lifetime of natural gas infrastructure. However, there would be costs associated with upgrading steel pipes to make them suitable for hydrogen transport, and for the eventual extraction of hydrogen from the gaseous mixture within.
CONCLUSION
The choice of green and blue hydrogen is important and often difficult, since both colors have differing prospects and considerations.
Green hydrogen is cleaner and can double as an energy storage medium during peak hours, which makes it more favorable for integration into the grid. Renewable energy is already among the least expensive sources of energy, and economies of scale will continue to push prices down. Coupled with rapidly increasing investments in electrolyzer manufacture, both capital and variable power costs for green hydrogen are likely to decrease. However, capital underutilization will remain an issue unless the demand for hydrogen is built up greatly to justify higher capacity electrolyzers, and/or stabilization measures (like short-term storage) are integrated into the power supply.
Blue hydrogen may find it increasingly difficult to retain its economic advantage. Future viability is dependent on the development of extremely low-cost CCS techniques, which must also show significant improvements in capturing efficiency (from about 65% to 95%). Natural gas prices will always majorly influence end-costs, making them vulnerable to volatility and geopolitical considerations, especially for net gas importers. However, blue hydrogen can be created by repurposing existing pipelines and SMR plants. So, it could serve as an effective transition while renewable capacity for green hydrogen production is stepped up and electrolyzer costs fall.
As James Watson, secretary-general of Eurogas said, “to realistically limit warming to 1.5° C by 2050”, we are “going to have to use CCS”. Both variants of hydrogen have to be deployed in conjunction, with the eventual goal of complete decarbonization in mind.